What are the Top 5 Mistakes to Avoid When Operating a Forklift
Avoiding These Mistakes Could Save Your Life
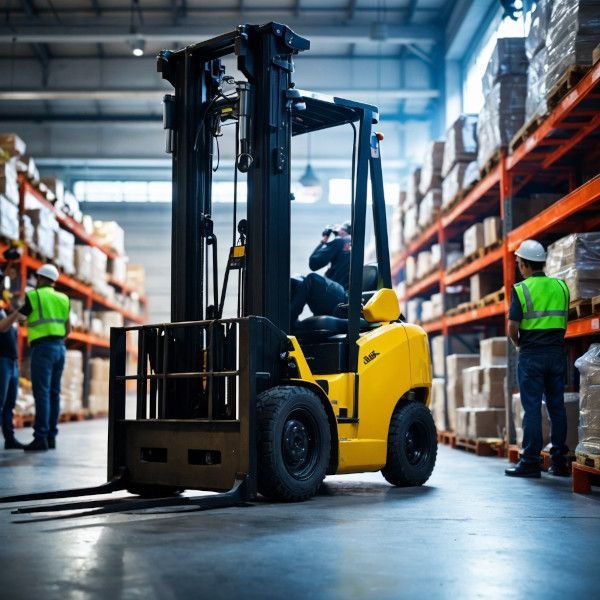
Neglecting Pre Operation Checks: Recipe for Trouble
In the operation of a forklifts pre operation checks play an important role in the safe and smooth handling of materials. While they are essential equipment in many industrial environments, forklifts can pose risks if not properly looked after. One crucial aspect is the operation check. Skipping an operation check can lead to severe accidents putting not just the operator at risk but also other workers and infrastructure. Recognising the significance and steps involved in these checks can greatly reduce hazards and promote a safe work environment.
The Significance of Pre Operation Checks
Pre operation checks are crucial for spotting issues before they become concerns. These checks act as a defence in maintaining forklift safety and efficiency. Detecting defects on helps prevent breakdowns during operation. This proactive approach is key to averting accidents that could cause harm, fatalities and substantial financial setbacks for the company.
Key Forklift Components to Examine Before Operation
An operation check should encompass various critical parts of the forklift. Each component needs inspection for any indications of damage wear or malfunction.
Tyres: Scrutinise the tyres for cuts, cracks or excessive wear and tear. Make sure to inflate the tyres to the recommended pressure levels for maximum performance. Uneven tyre wear can impact the stability of the forklift increasing the risk of tipping over.
Brake Test:
Check the brakes to ensure they are working correctly. Malfunctioning brakes can lead to difficulties in stopping the forklift on time potentially causing accidents and injuries.
Light Inspection: Confirm that all lights, such as headlights, brake lights and warning lights are functioning properly. Good lighting is essential for visibility in lit areas.
Hydraulic Systems:
Inspect the systems for leaks or any damage indications. Ensure that the hydraulic fluid levels are sufficient. Failure in systems can result in issues when lifting or lowering loads.
Safety Checks: Verify that safety features like the horn, seatbelt and backup alarm are operational. These features serve to alert others about the presence of the forklift and safeguard its operator.
Conducting Forklift Inspection
To perform an operatiing inspection follow these steps:
Visual Examination: Begin with visually inspecting the forklift for any visible signs of damage or wear. Look out for dents, cracks or structural problems on its exterior.
Operational Testing: After completing the check up proceed with tests.
Make sure to test the brakes, steering and hydraulic systems for any sounds that could signal an issue.
Functional Checks: Confirm that all safety features are working properly. Check the horn, lights and seatbelt functionality. Test the alarm and other warning devices.
Fluid Levels: Verify all levels such as engine oil, hydraulic fluid and coolant. Low fluid levels may cause mechanical problems.
Documentation: Keep a logbook of the inspection results. Note down any problems discovered and the steps taken to fix them. Maintaining records helps in tracking maintenance history and identifying recurring issues.
Advantages of Regular Inspections
Pre operation checks offer various benefits including ensuring forklift reliability thus reducing accident risks and prolonging equipment lifespan. They can also save money by preventing repairs and downtime. Neglecting pre operation inspections can lead to serious consequences. By performing these checks forklift operators can ensure their equipment is safe to use in all conditions. This proactive approach not only safeguards operators and colleagues but also enhances workplace efficiency and productivity.
Ensuring safety through regular inspections is a duty that should never be overlooked.
The Risks of Overloading Forklifts: A Hazard to Avoid
Forklifts play an essential role in warehouse environments serving to lift and transport heavy loads efficiently and accurately. However, their effectiveness relies on safe and correct handling particularly when it comes to load capacities. Overloading a forklift is a perilous error that can lead to serious accidents and harm. Recognising the dangers associated with overloading and following manufacturer instructions are vital for maintaining an efficient workplace.
The Hazards of Exceeding Limits
Going beyond a forklifts weight limit poses a serious safety risk. When overloaded, the stability of the forklift is compromised heightening the chances of tipping over. This not only jeopardises the operator but also puts other workers and equipment at risk in the area. A tipping forklift can cause damage, including crushing injuries, fatalities and substantial property damage. Hence, understanding and adhering to the load limits of the forklift is crucial.
Manufacturers Load Capacity Recommendations
Every forklift is accompanied by load capacity recommendations provided by the manufacturer. These recommendations are established through testing to ensure safe operations. The load capacity information, often displayed on the data plate of the forklift must be followed diligently at all times. It's important to take into account both the weight and size of the load as oversized loads can impact the balance and stability of the forklift.
Ensuring Distribution and Securing Loads on Forklift
Properly handling loads goes beyond just following weight restrictions. It's crucial to make sure that loads are evenly spread out and securely attached. A poorly distributed load can shift during transport leading to instability and potential tipping. Operators should position the load at the centre of the forks. They should then ensure it is balanced before lifting. Using securing methods, like straps or shrink wrap also helps prevent loads from shifting or falling during movement.
Avoiding Oversized Loads
Forklifts are restricted not by weight, but by the dimensions of the load they can handle safely. Large loads can obstruct the operators view making it challenging to navigate safely. They can also cause imbalances especially if they extend forward or sideways. Always verify that the load fits within the forklifts dimensions and doesn't exceed its height capacity.
Practicing Safe Lifting Techniques
Adhering to lifting practices is crucial to avoid overloading and ensure stability. Operators should:
Be Aware of Forklift Limits: Understand the forklifts load capacity. Refrain from estimating load weights. When unsure it's best to use a scale to check the weight of the load.
Ensure Load Stability: Before lifting, make sure that the load is stable and evenly distributed. Confirm that the load is centred and the forks are positioned correctly.
Employ Securing Techniques:
Use straps or shrink wrap to secure the load if needed. This helps prevent any movement and maintains stability during transportation.
Avoid Lifting Overhead:
Exercise caution when lifting loads to shelves or racks. Verify that the load doesn't surpass the forklifts lifting height capacity and remains stable at all levels.
Take it Slow and Steady: Drive the forklift at a safe speed especially when carrying large loads. Abrupt movements or sharp turns can lead to shifting of the load or tipping of the forklift.
Forklift Training and Awareness
Proper training is crucial for all forklift operators. Forklift Training programs should cover guidelines on load capacity lifting methods and risks related to overloading. Operators should be urged to stay alert and report any instances of overloading or unsafe practices they observe. Regular refresher courses can help maintain awareness and ensure adherence to safety protocols.
Overloading a forklift poses dangers with serious risks involved. By following the recommended load capacity guidelines set by manufacturers, ensuring an even distribution of loads and using lifting techniques, operators can prevent accidents and uphold a secure work environment. It is crucial to invest in training and nurture a safety-oriented culture to effectively reduce the risks associated with overloading forklifts. Remember, a key aspect of operating forklifts safely is to understand and respect their limitations and capabilities.
Improper handling of loads with a forklift poses a serious safety risk. It is a major cause of workplace accidents and injuries. Such incidents can lead to damaged goods and financial losses. They can also endanger the well-being of forklift operators and other employees. Adhering to correct load handling practices is vital for ensuring a productive work environment. Lets delve into why load handling matters greatly and explore the strategies to mitigate associated risks.
The Impact of Mishandling Loads
Mistreating loads can have consequences, such as:
Dropped Materials:
Unsecured or imbalanced loads can slip off the forks resulting in goods falling off. This can lead to damaged products, higher operational expenses and potential dangers for workers.
Damaged Goods: Improperly handling loads can cause damage to items that are fragile or valuable. Damaged goods can result in losses and disrupt supply chains and operations.
Injuries: The critical outcome of incorrect load handling is the potential for injuries. Falling loads can hit operators or other workers causing injuries or even fatalities. Furthermore, unstable loads may lead to the forklift tipping over creating more risks.
Best Practices for Load Handling
To mitigate these risks it is crucial to adhere to practices for proper load handling:
Ensure Forks are Fully Inserted Under the Load: It is vital for stability to have the forks fully inserted under the load. Incorrectly, or uneven inserted forks may cause the load to become unbalanced increasing the risk of tipping or dropping. Operators should adjust the fork width according to the loads size. Ensure that the load is centred on the forks.
Check Load Stability:
Before lifting, verify that the load is stable and secure. Unstable loads might shift during transport resulting in accidents. If there are indications of instability in the load take precautions to secure it by using straps or shrink wrap.
Avoid Lifting Unstable Loads: Refrain from lifting improperly stacked loads. If a load is leaning or appears uneven it should be stabilized before lifting.
To minimise the chances of accidents it's important to follow safety protocols when handling loads with a forklift.
Ensure Clear Visibility: Having a clear line of sight is crucial for load handling. Make sure there are no obstructions blocking your view while moving or lifting loads. If visibility is compromised use a guide to assist you in navigating the forklift. Keeping clear visibility helps prevent collisions and allows for manoeuvrability.
Exercise Caution During Stacking and Unstacking: Extra care should be taken when stacking and unstacking loads. When stacking, ensure each layer is stable and evenly distributed. Avoid stacking loads unevenly as it can compromise stability. When unstacking, lower the loads cautiously to avoid any shifting or tipping incidents.
Follow Weight Limits: It's essential to adhere to the weight capacity limits specified for the forklift. Overloading the forklift can lead to instability and an increased risk of tipping over. Refer to the manufacturers guidelines. Make sure that the load weight falls within operating limits.
Maintain a Steady Pace: Abrupt movements, like turns or sudden accelerations can cause loads to shift or topple over. Operate the forklift at a controlled speed especially when transporting large items. Smooth movements contribute to load stability and help reduce accident risks.
Proper training plays an important role in ensuring the handling of loads. Forklift operators should undergo training programs that cover techniques for safe handling of loads, safety procedures and equipment operation. Regular refresher courses help reinforce practices and keep operators informed about safety protocols.
Moreover, promoting a culture of improvement can improve safety standards. Encouraging operators to report any issues or near misses related to load handling is important. Analysing these reports can help identify recurring issues and lead to the development of better handling techniques.
Mishandling loads poses many risks with strong consequences in the workplace. By adhering to safe work and operating practices and receiving proper training, forklift operators can handle loads safely and effectively. Prioritising load stability, ensuring visibility and following weight restrictions are essential steps in preventing accidents and injuries. A commitment to safe load handling not only safeguards workers but also contributes to the overall efficiency and success of the operation.
Neglecting Safety Protocols: A Vital Oversight
In warehouses, factories and construction sites, forklifts play a central role in material handling. These powerful machines come with risks that require adherence to safety measures. Failing to follow safety protocols can result in accidents, injuries and even loss of life. Here we will examine the significance of observing safety guidelines and the effective ways to maintain a work environment.
The Significance of Safety Protocols
Safety protocols are put in place to minimise risks and safeguard both the forklift operator and those in their vicinity. These guidelines are formulated based on research and practical experience addressing hazards associated with forklift usage. By adhering to these protocols organisations can significantly decrease the chances of accidents occurring and promote a workplace.
Essential Safety Measures to Abide By
Using a Seatbelt: Among the most important safety precautions is wearing a seatbelt while operating a forklift. In case of a tip over a seatbelt can prevent the operator from being ejected from the vehicle thereby reducing the likelihood of harm or fatality. Despite its simple nature overlooking this safety measure is a mistake that can lead to disastrous outcomes.
Adhere to Speed Limits:
Operating a forklift at high speeds can be dangerous as it increases the risk of accidents such as losing control, tipping over or hitting obstacles. Speed limits are set considering the workplace and the forklifts capabilities. It's important for operators to stick to these limits and adjust their speed based on factors like spaces or areas with lots of foot traffic.
Stay on Forklift Paths: Forklift travel paths are designated to keep forklifts separate from areas where pedestrians walk reducing the chances of accidents. Operators should always use these paths. Avoid taking shortcuts through crowded pedestrian zones. Clear signs and floor markings help guide operators along these routes.
Follow all Safety Protocols: Safety protocols cover procedures including load handling and regular equipment checks. Following these protocols ensures that the forklift is used safely and effectively. Pre operation inspections help catch issues while correct load handling techniques prevent accidents caused by unstable loads.
Be Aware of Your Surroundings: When operating a forklift it's crucial to be aware of your surroundings at all times. Operators need to stay alert to workers, obstacles and changes, in the environment. This awareness is crucial in preventing accidents as it enables operators to anticipate and respond to dangers. It is important to be extra careful when making turns, reversing or navigating through busy areas.
Being Cautious in Confined Spaces:
Manoeuvring through tight spaces poses its set of challenges. Operators should proceed with care using speeds and precise movements to avoid any collisions. Utilising mirrors and spotters can enhance visibility. Ensure navigation in these limited areas.
The Ramifications of Disregarding Safety Protocols
Neglecting safety protocols can result in severe consequences, such as:
Accidents and Injuries: The primary outcome is the heightened risk of accidents and injuries. These incidents can lead to severe injuries impacting the well-being of both the operator and others involved.
Damage to Property:
Collisions and tip overs can cause harm to the forklift, infrastructure and goods being transported. This damage may necessitate repairs and operational downtime.
Legal and Financial Penalties:
Negligence related accidents may trigger repercussions and financial penalties for the organisation. Adhering to safety standards helps organisations steer clear of these outcomes.
Decreased Efficiency: Accidents and equipment damage disrupt operations hampering productivity. Conversely a secure work environment fosters seamless workflow. These rules are put in place to make sure that skilled individuals operate forklifts reducing the chances of accidents. Not following these guidelines can lead to fines, legal responsibilities and closer monitoring by regulatory bodies.
Insufficient Training: Apart from meeting regulatory or government standards the main goal of forklift training is safety. Insufficient training can result in mishaps like collisions, tip overs and spills of loads. These incidents can cause injuries or even fatalities, damage to property and disruptions in operations. Adequate training provides operators with the skills to navigate these risks effectively and create a work environment.
Essential Elements of Comprehensive Forklift Training
Foundational Operational Training:
This core training covers the basics of operating a forklift, including starting and stopping the vehicle steering it lifting and lowering loads and manoeuvring in confined spaces. Operators learn how to use the controls of the forklift and understand its capabilities as limitations.
Safety Measures: A significant part of forklift training emphasises safety protocols. Operators are educated on conducting operation inspections identifying and avoiding hazards and adhering to established safety measures. This training also includes techniques for handling loads such as ensuring load balance and securing them before lifting.
Adherence to Regulations: Grasping regulations and complying with them is a component of forklift training.
Operators should have an understanding of the requirements related to operating forklifts in their area including the need for certification and licencing.
Practical Hands On Training: It's important for operators to undergo hands on training to gain the skills and confidence needed to operate a forklift. Working under the guidance of experienced trainers, operators practice manoeuvring the forklift, handling loads and carrying out maintenance tasks.
Emergency Response Procedures: Training should also cover what actions to take in case of emergencies like tip overs, fires or other accidents. Knowing how to react and correctly can help reduce the impact of an incident and prevent harm.
Why do You Need Ongoing Training and Refresher Forklift Courses
Forklift training is not a one-time affair. Continuous training and periodic refresher courses are essential to ensure that operators are aware of practices, safety protocols and any regulatory changes. With time, operators may develop bad habits and become complacent increasing the likelihood of accidents. Refresher courses serve to reinforce procedures and highlight any safety updates.
Ongoing training also acknowledges the changing landscape of forklift technology. With new models and features being introduced regularly, it's crucial for operators to stay informed about how to utilise these advancements. Continuous education guarantees that operators can make use of technology effectively to enhance safety and productivity.
The Benefits of Forklift Training for Organisations
Choosing to invest in forklift training brings a range of advantages for companies, such as:
Improved Safety:
Well-trained operators have a lower likelihood of getting into accidents creating a safer work environment. This helps reduce the chances of injuries and fatalities safeguarding both employees and the company’s image.
Enhanced Efficiency:
Skilled operators can operate forklifts effectively cutting down on the time required for handling materials and minimising downtime caused by accidents or equipment issues.
Cost Efficiency: With less accidents there are reduced costs related to bills, legal expenses, equipment repairs and insurance premiums. Adequate training also aids in preventing damage to goods and structures leading to savings.
Regulatory and Fine Avoidance: Following training and certification mandates ensures that organisations comply with regulations avoiding fines and legal entanglements. Insufficient forklift training poses safety risks and operational challenges. Ensuring that all forklift operators receive training and certification in line with laws is crucial in managing these risks. Ongoing training sessions and refresher courses help keep operators up to date on practices and changing safety standards fostering a culture of safety consciousness and competence. By investing in training initiatives businesses can improve safety standards boost productivity levels and realise lasting financial benefits.
For all you forklift training requirments call EDB Training Services
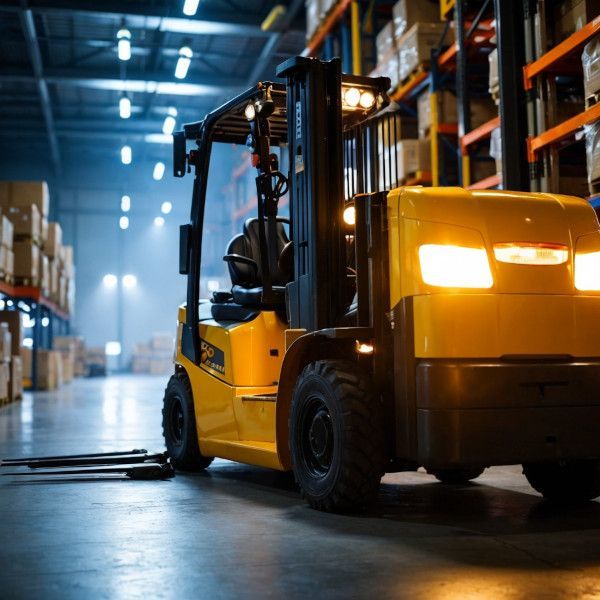